Fast acquiring and analysis of three dimensional laser range data
Hartmut Surmann, Kai Lingemann, Andreas
Nüchter and Joachim Hertzberg
FhG AiS - Fraunhofer Gesellschaft
Institute for Autonomous
intelligent Systems,
Schloss Birlinghoven,
D-53754 Sankt Augustin, Germany,
{surmann
lingemann
nuechter
hertzberg}@ais.fraunhofer.de
VMV 2001, Stuttgart, 21 - 23 Nov. 2001
Abstract:
This paper presents a precise (

1cm), lightweight (5kg) and low cost 3D laser range
finder for the fast gaging (

sec) of environments.
Real-time algorithms for the data reduction,
3D-object segmentation are also presented.
A special designed suspension unit, a standard servo motor and a
standard 2D range finder are used to build the 3D scanner.
Maximal resolutions e.g. 180 (h)

90 (v) degree with 194400
points are grabbed in 8.1 seconds and low resolutions with 16200
points are grabbed in 1.4 seconds.
While scanning, different online algorithms for line and surface
detection are applied to the data. 3D-Object segmentation and
detection are done offline after the scan. With the proposed
approach, a precise, reliable, mobile, low cost, and real-time
capable 3D sensor for the contact-less measuring of environments
without additional landmarks is available.
Range image acquisition can be defined as the process of
determining the distance (or depth) from a given observation
point to all points of consideration in a scene. The technology
of laser range finders is not new and has been used for many
years in military and airborne remote sensing survey
applications. Many systems are available for a wide range of
applications, for example land surveying, quality control, and
civil engineering.
An important issue for man made environments is the choice
of the sensor type from which raw range information from the
scene is obtained.
Today's commercial 3D laser range finders are large and heavy,
build for stationary use mainly.
This paper presents a mobile 3D laser range
finder. (fig. 1). The scanner is built on the base of a
commercial 2D laser range finder from Schmersal together with a
special designed suspension unit and a standard servo
motor1 (1). The 2D scanner is very fast (processing
time
15 ms), precise (
1 cm,
) and becoming
cheaper (
$3000) since different competing products
e.g. 3 (3); 2 (2) are available.
Figure 1:
The 3D laser range finder. The servo is
mounted at the left side.
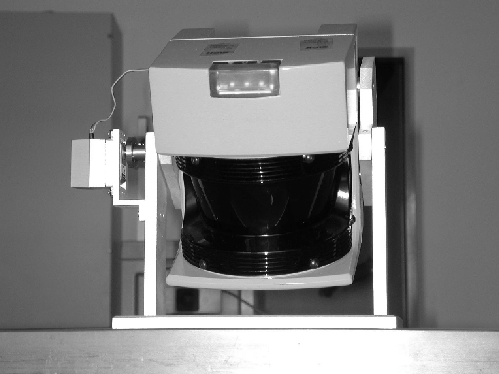 |
A few number of scientific groups develop fast, lightweight and mobile
3D laser range finders and/or special algorithms on the basis of 2D
laser range finders to overcome the drawback of only 2D proximity
information 7 (7); 6 (6); 5 (5); 4 (4). Thrun et
al. use two laser range finders, one rotated by 90 degrees
5 (5). The 3D information is generated while the robot
is moving. The accuracy of the acquired data depends on the accuracy
of the robot pose. 3D-Object detection without moving the robot is not
possible. Waltheim et al. 7 (7) and Kristensen et
al. 6 (6) use an amtec rotation module
8 (8) with high accuracy at high costs (
$3500).
The presented 3D laser range finder is built on the basis of a 2D
range finder by extension with a mount and a servomotor. The 2D laser
range finder is attached to the mount for being rotated. The rotation
axis is horizontal. A standard servo (
$75) is connected on the
left side (fig. 1). Annotation: An alternative approach
is to rotate the range finder around the vertical axis. Throughout
this paper we will only discuss the approach based on a horizontal
rotation, all presented algorithms can be used in the same way. The
differences between both approaches are the orientation of the apex
angle and the effects of dynamic objects moving through the scene,
e.g. persons. Using vertical scanning, a perturbation either appears
with low probability within a few scans making them useless for
further data processing, or does not appear at all. The first
approach on the other hand shows perturbations throughout the whole
scene, but these data can still be used for robot navigation and
object detection.
Due to the flexible setup we can connect different 2D laser range
finders (Schmersal 3 (3), Sick 2 (2)). This
leads to a wide variety of scan resolutions and scan speeds (see
tab. 1) - the latter also depending on the used serial
device. The used laser range finder (max. scanning distance 60m) can
also be used outside of buildings (see fig.2).
Table 1:
Comparison between Schmersal 3 (3) and Sick 2 (2) laser scanner,
connected to two different serial devices.
|
| |
Schmersal |
Sick |
points |
| low |
11250 |
16200 |
|
| maximal |
135000 |
194400 |
RS232 |
| low |
5.4 sec |
5.6 sec |
|
| maximal |
48 sec |
67.5 sec |
RS422 |
| low |
5.4 sec |
1.35 sec |
|
| maximal |
16.2 sec |
8.1 sec |
resolution (hor.) |
5 cm |
1 cm |
|
resolution (rot.) |
1 |
1 |
|
|
The given setup determines an intrinsic order of the acquired
data. The data coming from the 2D laser range finder is ordered
anticlockwise. In addition the 2D scans (scanned planes) are ordered
due to the rotation.
The 3D laser range finder uses only standard computer interfaces.
The servomotor is directly connected to the parallel port, the 2D
laser range finder to the serial port and the camera is
connected to an USB port. Nowadays, every computer (esp. laptops) does
have these interfaces and therefore the built 3D laser range finder can
be used easily on mobile platforms.
The mount and the servo are inexpensive and no special electronic
devices are used, so the price of the whole system mainly depends
on the used 2D laser range finder.
Figure 2:
Schloss Birlinghoven.
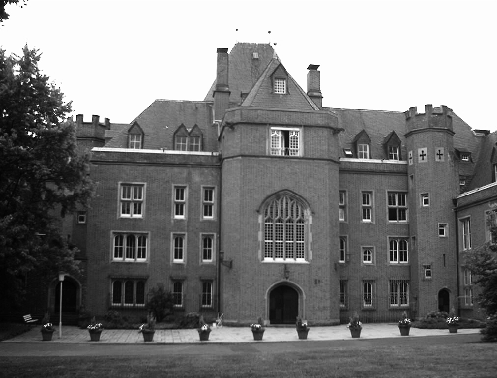 |
Figure 3:
3D scan of Schloss Birlinghoven, scan time 48 sec with
the schmersal scanner over RS232.
 |
The servo of the new 3D laser range finder is controlled by a
computer running RT-Linux, a real-time operating system which runs
LINUX as a task with lowest priority. The servomotor expects a signal
every 20 ms, the length of the signal determines the position of the
motor (1 ms = leftmost position, 1.5 ms = middle position, 2 ms =
rightmost position). This very time critical job has to be done by a
real-time operating system, since a latency of about 10
s corresponds
to a deviation of
. Real-time Linux has an average latency of
about 5
s (PII-333) and thus the rotation can be realized
with an average deviation of
.
Online algorithms for line detection
While scanning, different online algorithms for line and surface
detection (LENCOMP & HOUGH & LINMER) are applied to the data, thus no extra processing time is
needed. Two different kinds of line detection algorithms have been
tested 10 (10); 9 (9).
Figure 4:
Line detection applied to a scan slice
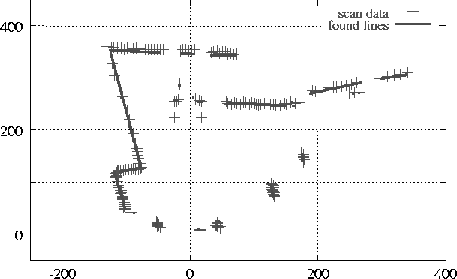 |
The first algorithm (LENCOMP) is a simple straightforward matching algorithm
running in
(
the number of points), with small
constants. The algorithm implements a simple length comparison. The
data of the laser range finder (points
) is ordered
anticlockwise so that one comparison per point is sufficient. We assume
that the points
are already on a line. For
we have to check if
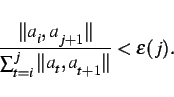 |
(1) |
To obtain better results this algorithm runs on preprocessed
data. Data points located close together are joined so the distance from
one point to the next point is almost the same (reduction filter). This process minimizes
the fluctuations within the data and reduces the points to be processed.
Hence this algorithm runs very fast, but the quality of the lines is
limited.
The second line detection algorithm implemented is the well known
Hough Transformation 12 (12); 11 (11) (see fig. 4). A
(
) parameterization of the space of lines is used, where
is the angle of the normal to the line and
the
distance along this normal from the line to the origin of the image. A
transformation of every point
results in a histogram. The
maximum of the histogram corresponds to a line and the number of
points belonging to this line is maximal.
The iteration of the following three steps returns all line segments.
- find maximum = find straight line and calculate the line equation

- tag all points belonging to this line
- remove these points from the histogram and make line segments
The final step uses the intrinsic order of the data as it comes from
the laser range finder. Due to this intrinsic order only one check is
necessary to determine whether a point belongs to a line segment. An
advantage of the Hough transformation is that it computes the general
line equation and all of the belonging line segments in one step which
is helpful in further processing steps i.e. 3D surface and 3D
object detection.
The Hough-Transformation runs in
), with
the
distance to the furthest data point. This maximum distance is currently
limited to 10 m, so that the transformation can be done in real-time. For
indoor environments this limitation is sufficient.
After line detection the transformation of the 2D coordinates into 3D
coordinates is done (fig. 5). All following data processing steps operate on
the three dimensional data.
Figure 5:
Composed 3D image from line detection done in 2D planes.
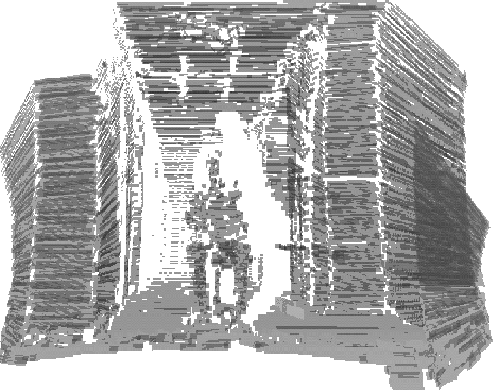 |
All algorithms described so far run on 2 dimensional data. After line
detection is done the data is converted into 3D. Based on the
detected lines, the following algorithm LINMER detects
surfaces in the 3-dimensional scene.
Scanning a plane surface, the line detection algorithm returns a
sequence of lines in successive 2D scans approximate the
shape of this surface. Now, the task is to recognize such structures within
the 3D data input and to concatenate these independent lines to one
single surface. The surface detection algorithm LINMER proceeds the
following steps:
- The first set of lines - coming from the very first 2D scan - is
stored.
- Every other line is being checked with the set of stored lines. If a
matching line is found, these two lines are transformed into a
surface.
- If no such matching line exists, the line may be an extension of an
already found surface.
In this case, the new line is matching with
the top line of a surface. This top line is being replaced by the new
line, resulting in an enlarged surface (fig. 6).
- Otherwise the line is stored as a stand-alone line in the set
mentioned above.
To achieve real time capabilities, the algorithm makes use of the
characteristics of the data as it comes
from the range finder, i.e. it is the order by the scanned planes.
Therefore the lines are sorted throughout the whole scene (with regard
to their location within the virtual scene) due to their inherited
order. Thus an efficient local search can be realized.
Three criteria have to be fulfilled in order to match lines: First the
angle between the two lines has to be smaller than a given value
. Second the endpoints of the matching line must be within an
-area around the corresponding points of the given line
(fig. 6). The first constraint is necessary for correct
classification of short lines, since they fulfill the distance
criterion very easily. To match a line with a surface these two
constraints have to hold between the last line of the surface an the
new line taken into account. In addition we apply a third constraint
that is the line has to lie approximately in the plane given by the
surface.
Figure 6:
Expansion of a surface by a new line
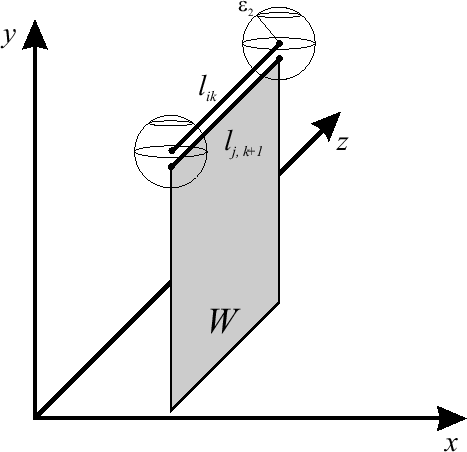 |
This step, merely a joining of lines found in former scans, can be
done online, too, since no data from future scans is necessary. This
means that the robot or a user gets much 3D information about objects in
the scenery right during the scan.
Offline algorithms (POLYGEN & O-SEG) are used to create a 3D map of the room and
to enable a safe navigation of the robot. Despite of the prior
algorithms, this step requires information about the whole
scene and has to be done after the scan process is finished.
The surface detection routines creates surfaces consisting
of lines. Since the quality of the lines is limited due to noise of
the scan data, the result of the surface detection are small surfaces
which may even overlap. The task of polygon creation is to merge
these surfaces to polygons.
Polygon detection is divided into three steps:
- First the LENCOMP algorithm (sec. 3.2) uses the
endpoints of all lines of a surface to
detect 3D edges. This transforms
the line strips into polygons.
- After it, each polygon is projected form the 3D coordinate space into a 2D
coordinate space of the plane given by the polygon.
- Now, the polygons are merged. Since the polygons may overlap this step has
to create an overall polygon. The algorithm from Vatti 13 (13)
is used as a polygon clipping algorithm.
Each polygon can be a single polygon or a polygon set. Each individual
polygon in a polygon set may be convex, concave of
self-intersecting. Clipping is defined as interaction of the so called
subject polygon and the clipping polygon, hence it is also usable for
2D Boolean operations, e.g. union. If two polygons are approximately
within the same plane, these polygons at a time are clipped.
The polygons are striped from bottom to top. Each strip is a
horizontal (with respect to the 2D polygon coordinate system) sweep,
that is an area between two successive horizontal lines from a set of
horizontal lines drawn through all the vertices. During the striping
the local maxima and minima are determined, vertices and intersections
are classified. From this classification Vattis algorithms computes in
our case the overall polygons.
Vattis algorithm runs in linear time in the number of edges of the
subject and clipping polygon.
The polygon merging algorithm is also used to merge polygons from
different scans
resulting in a complete surface model of the environment.
As a final step the generated polygons (convex or concave) are
transformed into triangle strips only to visualize them in
OPENGL.
Figure 7:
3D image formed of polygons.
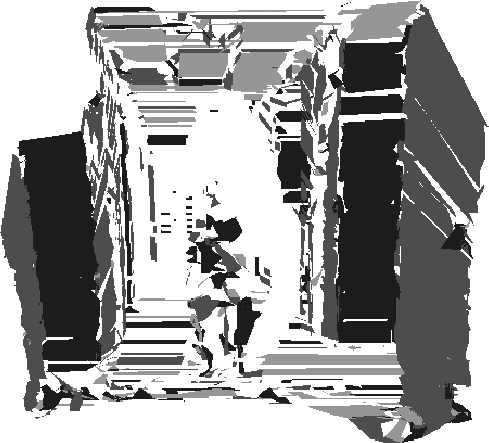 |
Figure 7 shows the result of the polygon merging step
applied to the scan shown in figure 5
3D-Object segmentation (O-SEG) is done by sequentially merging conglomerations of
3D-points, 3D-lines and 3D-surfaces into one 3D-object:
- Start with one arbitrary element, i.e. a large 3D-surface. This element
is already treated as a ``real'' 3D-object in this state of the
algorithm.
- Iterate over the previously found elements and check whether there are
any elements ``near enough'' to this object. This ``near'' constraint
is given by the setup, e.g. one should merge only elements closer than
the size of the robot, since the robot can't pass through such
objects.
- If such an element is found, the object is enlarged until it
encloses this element.
- Repeat until no more elements fit the given object.
During this process, all elements belonging to the object are
marked. The object segmentation algorithm starts again, until no more
conglomerations of elements exists, i.e. until no more objects can be
found within the scanned scene.
Figure 8:
Representation of an object
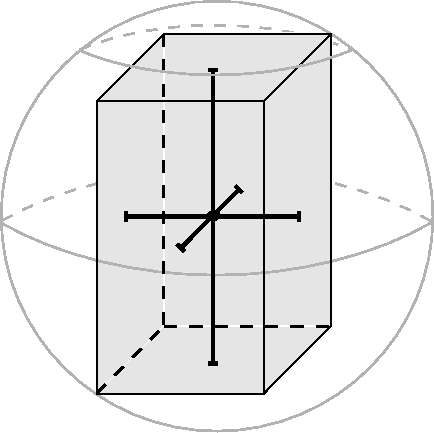 |
The objects are characterized by bounding boxes (cubes) (fig.
8). A bounding box is given by 3 orthogonal lines,
corresponding to the axes of the virtual world coordinate system.
In addition, each object is surrounded by a sphere which encloses the
whole bounding box. This sphere is used to check very fast
whether a single point is near enough to this object to be
examined as part of the bounding box.
The O-SEG algorithm first checks if the point is inside the sphere. This can
be done by testing the euclidian distance. If the element passes
this test, the algorithm determines whether the point is
near enough to the actual bounding box. In this case, the lines
defining the bounding box have to be re-adjusted to enclose this new
point, the sphere likewise.
This procedure can be generalized to handle other kinds of elements as
well, since lines are represented by 2 points and surfaces by 2 lines.
To visualize the data, a viewer program 2SHOW based on
OPENGL was implemented. The task of this program is the
projection of the 3D scene to the image plane, i.e. the monitor.
A graphical user interface J42SHOW (fig. 9) developed with JAVA
enables a simple and easy way to use the scanner application.
Figure 9:
JAVA user interface
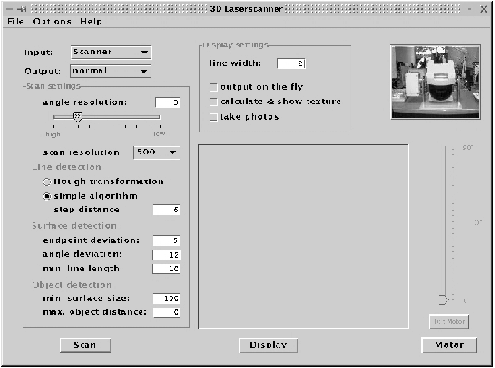 |
The viewer program can easily be controlled by an extern JAVA panel
(fig. 10 & 11).
It enables the user to select the element types that are drawn (points, lines, surfaces and
objects), to navigate through the 3D scene, to use a simple VCR interface
and to extract further information about the scene:
clicking on an element returns position, size and - depending on the type of the element -
data like number of points within the object, etc.
Figure 10:
Navigation controlling panel.
 |
Figure 11:
Object informations box.
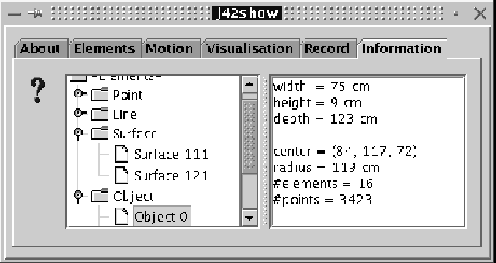 |
Figure:
Application as body scanner a).
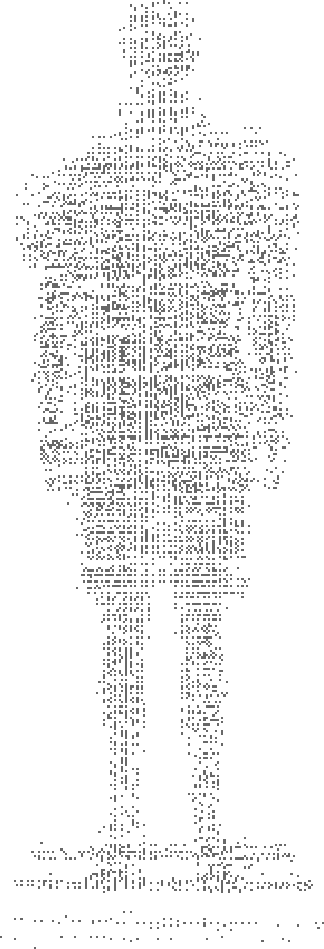 |
Figure:
Application as body scanner b).
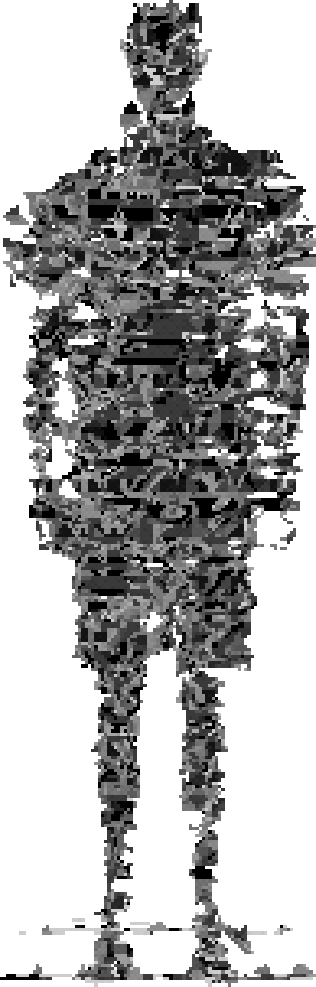 |
An example (fig. 13 & 14)
visualizes the performance of the
scanner and the implemented algorithms. It shows the 2nd author taking
a video in a corridor and two different views of the scanned
scene.
The scene was scanned in 12 seconds (schmersal scanner). During the 12 seconds
the 115000 data points were reduced to 2596 lines and 977 surfaces.
The door on the right side as well as some parts of the walls are
detected as flat surfaces
.
Another interesting application is the use of the 3D laser range finder as
a body scanner (fig. 12).
After the scanning process, 180 polygons are created containing
only 1144 data points. In addition 60 objects are detected in 2.5
seconds.
This paper has presented a mobile, low-cost, precise and reliable high quality 3D
sensor.
The 3D laser is built on
base of an ordinary 2D range finder and uses only standard computer
interfaces.
The 3D scanner
senses the environment contact-less without the
necessity of setting landmarks.
The scan resolution for a complete 3D scan of an area of 180 (h)
90 (v) degree is up to 194400 points and can be grabbed in 8.1
seconds. The precision is mainly determined by the laser scanner (
1 cm).
Low resolutions e.g. 180 (h)
90 (v) degree with 16200
points are grabbed in 1.4 seconds.
While scanning, different online
algorithms for 3D-line and 3D-surface detection are applied to the
data. 3D-Object segmentation and detection are done offline after the
scan.
Several products and applications benefits
from our 3D laser range finder because it is light, small and
very fast:
- Autonomous mobile robots.
Due to the light weight of the 3D scanner it can be used by
mobile robots to survey the
environments and to build a precise map. The robots can also
detect and avoid complicated obstacles e.g. overhanging
obstacles which could not be recognized by 2D distance
sensors. Furthermore, all kinds of docking maneuvers even
in complicated locations can be done autonomously 14 (14).
- Control systems. They uses the 3D information
from the scanner to detect and classify objects.
Especially machines can be supervised and switch off if humans
are in their working area (3D zone defense with a 3d laser
range finder).
- Facility management systems. Facility management systems
require up-to-date informations of the facilities.
Especially a complete digital building model which is
continuously updated is demanded. The 3D scanner mounted
on an autonomous mobile robot can be used to build and update
digital building models. Property Management Systems can
be used more effectively and more cheaply.
Figure 13:
Example of a scanned scene
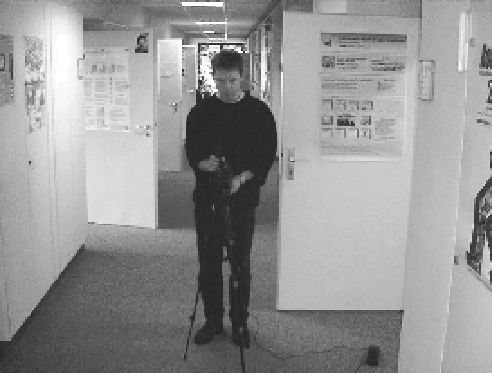 |
Figure 14:
Two
different views on the example scene of figure 13.
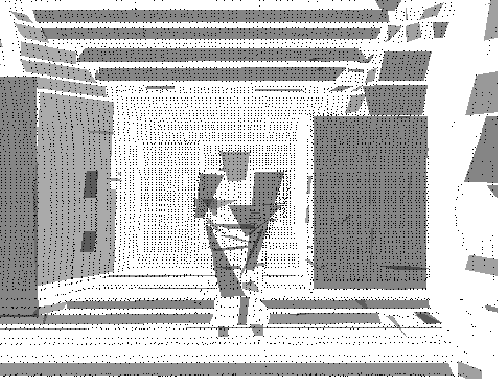 |
Figure:
Two
different views on the example scene of figure 13.
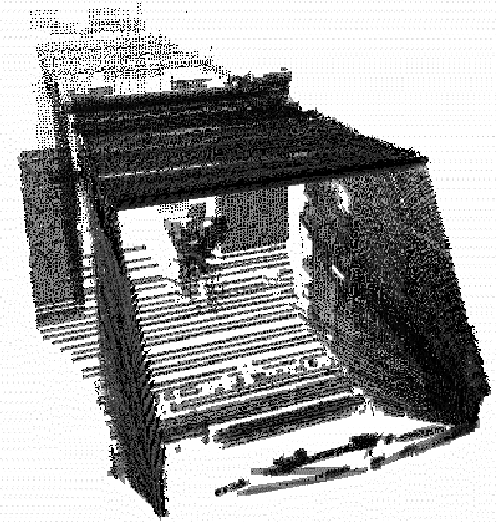 |
Acknowledgment Special thanks to Stefan Materne and the unknown reviewers
for hints and corrections.
-
Andreas Nuechter Hartmut Surmann, Kai Lingemann and Joachim Hertzberg,
- ``A 3d laser range finder for autonomous mobile robots,''
in Proceedings of the of the 32nd ISR (International Symposium
on Robotics), Seoul, 2001, pp. 153 - 158.
-
URL: Sick optic electronic,
- ``PLS: Definition der Telegramme zwischen
Benutzerschnittstelle und Sensorsystem über RS-422 /
RS-232,''
in http://www.sickoptic.com/laser.htm, 2000.
-
URL: Schmersal EOT,
- ``LSS 300: Telegramm zwischen Benutzerschnittstelle
und Sensorsystem V.1.14,''
in http:// www.schmersal.de/d/produkte/n2000/laserlss.html,
2000.
-
S.F. El-Hakim, P. Boulanger, F. Blais, J.A. Beraldin, and G. Roth,
- ``A mobile system for indoor 3-d mapping and positioning,''
in Proceedings of the International Symposium on Real-Time
Imaging and Dynamic Analysis, Hakodate, Japan, 1998, pp. 331 - 338.
-
Sebastian Thrun, Dieter Fox, and Wolfram Burgard,
- ``A real-time algorithm for mobile robot mapping with applications to
multi-robot and 3d mapping,''
in IEEE International Conference on Robotics and Automation, San
Francisco, 2000.
-
Steen Kristensen and Patric Jensfelt,
- ``Active global localisation for a mobile robot using multiple
hypothesis tracking,''
in Proceedings of the IJCAI'99 Workshop on Reasoning with
Uncertainty in Robot Navigation, Stockholm, Sweden, 1999, pp. 13-22.
-
Axel Walthelm and Amir Madany Momlouk,
- ``Multisensoric active spatial exploration and modeling,''
in Dynamische Perzeption: Workshop der GI-Fachgruppe
1.0.4 Bildverstehen, Ulm. 2000, pp. 141-146, AKA Akad. Verl.-Ges.,
Berlin.
-
URL: amtec,
- ``amtec product homepage,''
in http://www.powercube.de/index_products.html,
1999.
-
Michael Pauly, Hartmut Surmann, Marion Finke, and Nang Liang,
- ``Real-time object detection for autonomous robots,''
Informatik Aktuell. Autonome Mobile Systeme, 14.
Fachgespräch, Springer-Verlag, pp. 57-64, 1998.
-
J.-S. Gutmann,
- Robuste Navigation autonomer mobiler Systeme (in German),
Doctoral Thesis,
Akademische Verlagsgesellschaft Aka, Berlin, 2000.
-
P. V. C. Hough,
- ``Methods and means for recognising complex patterns,''
in U.S. Patent 3 069 654, Dec 1962.
-
R. A. McLaughlin and M. D. Alder,
- ``The hough transform versus the upwrite,''
IEEE Trans. Pattern Analysis and Machine Intelligence, vol. 20,
no. 4, pp. 396-400, 1998.
-
Bala R. Vatti,
- ``A generic solution to polygon clipping,''
Communications of the ACM, , no. 7, pp. 56-63, 07/1992.
-
Günther Schmidt Joachim Horn,
- ``Continuous localization of a mobile robot based on
3d-laser-range-data, predicted sensor images and dead-reckoning,''
Robotics and Autonomous Systems, vol. 14, pp. 99 - 118, 1995.
... surfaces
The 3D scene can be seen at
http://www.ais.fraunhofer.de/ARC/3D/
Hartmut Surmann
2001-10-17